I've seen some shafts with a cutaway in the bearing area near the big oil holes. Most are subtle but some are quite noticeable. If anyone knows better please chime in.
Here's my best guess:
+more cooling from increased drainage
+less bearing seep from lower pressure
+Faster spool and top speed from decreased surface area
-increased wear from less surface area and lower oil pressure
Here's my best guess:
+more cooling from increased drainage
+less bearing seep from lower pressure
+Faster spool and top speed from decreased surface area
-increased wear from less surface area and lower oil pressure
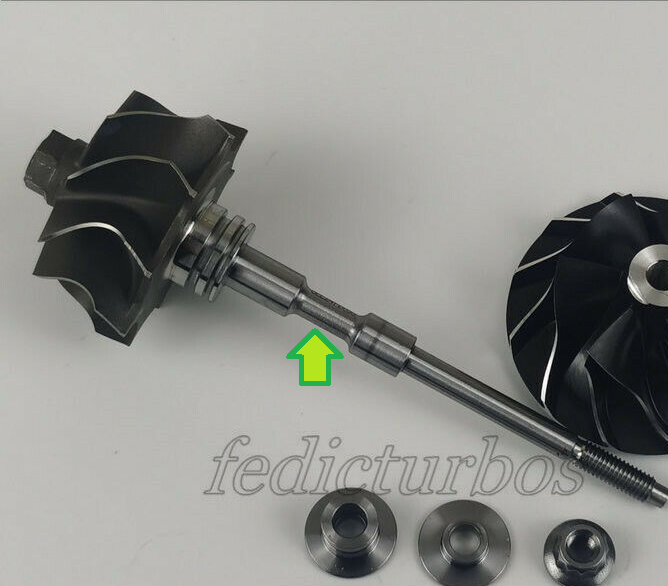
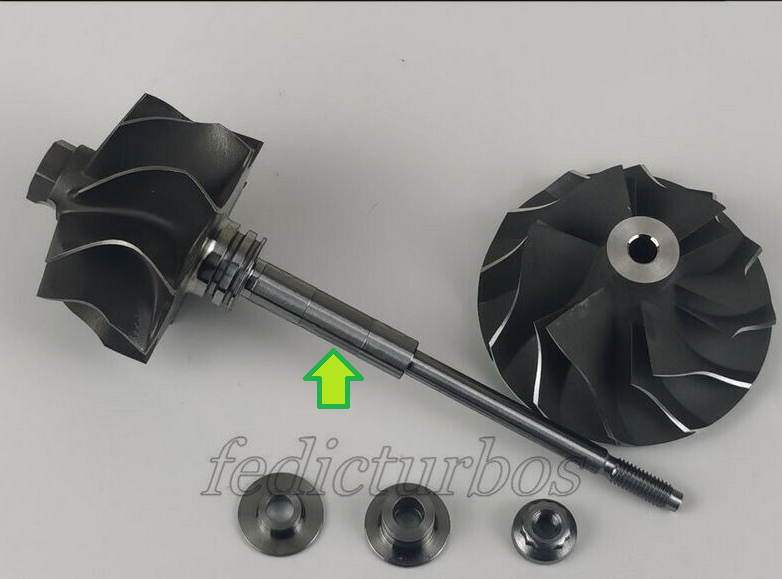